Interior
At Avery Dennison, we keep up with the latest automotive interior trends so that you don’t have to. Our expertise and global scale enable us to deliver innovative, sustainable and intelligent solutions for automotive interiors to suppliers all over the world. Discover the possibilities with Avery Dennison Performance Tapes.
Broad application range
Avery Dennison offers a comprehensive portfolio of adhesive solutions designed to meet the diverse needs of various industries, with a particular focus on automotive interiors. Our performance tapes have become the preferred alternative to traditional liquid adhesives, proving their value across a wide range of applications. From bonding and laminating to solving critical issues like Noise, Vibration, and Harshness (NVH), our products provide reliable, long-lasting solutions that enhance interior design and ensure safety.
Advancing automotive from the Chemicals Strategy for Sustainability
The CSS, launched in 2020, is a comprehensive package of measures designed to accelerate the transition towards a greener, cleaner economy. It’s already impacting the automotive interior sector by driving efforts to reduce chemical emissions.
OEMs and tier suppliers must adapt to these new regulations, and Avery Dennison's performance tapes, including our innovative UV acrylic adhesives and hotmelt rubbers, provide the solutions needed for the industry of tomorrow.
Interested in learning more about the EU Chemicals Strategy for Sustainability (CSS) and our work in developing solutions for performance tapes? Download our white paper, ‘The EU Chemical Strategy for Sustainability and its implications for automotive interior manufacturers’.
Applications
In automotive applications, our adhesives address key concerns like buzz, squeak, and rattle (BSR) issues, meeting many OEM specifications. As the industry transitions toward electric vehicles, there is growing demand for innovative flooring and carpet systems, as well as premium soft trim components. Avery Dennison’s bonding tapes are engineered to provide superior performance on the variety of surfaces and materials found inside vehicles, ensuring a premium driving experience. Our online OEM certification finder helps customers select the ideal adhesive tape for specific substrates, ensuring optimal performance for each application.
How EU’s CSS is setting the pace for innovation in automotive interiors
Written interview
The EU’s Chemicals Strategy for Sustainability (CSS), launched in 2020, is a wide-ranging package of measures designed to accelerate the move towards a greener, cleaner economy – and it’s already having an effect on the automotive interior sector. We talk to Michel Ravers, Technical Service Manager at Avery Dennison, about the objectives of the CSS, and the role that performance tapes are playing in helping OEMs and their suppliers get ready for the restrictions on chemical use that will inevitably follow.
About the interviewee
Michel Ravers
Application Technical Service Manager
Michel joined Avery Dennison in 1990 as part of the R&D team. For 24 years he has been active in development of adhesives & tapes for automotive and industrial applications.
After R&D he moved into a technical service role for automotive and industrial customers and since 2 years he's leading the European technical service team.
Contact:
michel.ravers@eu.averydennison.com
-
First, let’s have some background. What is the CSS?
It’s basically a package of over 80 actions that aims to protect citizens and the environment from harmful chemicals, while at the same time helping businesses move towards safer and more sustainable alternatives.
The CSS was published in 2020, and many of these actions are now being implemented, all overseen by a roundtable of stakeholders to make sure the objectives are achieved.
-
And what are those objectives?
There are numerous parts to it, but the two key ones are strengthening certain aspects of chemicals legislation, and supporting innovation for safe and sustainable chemicals.
Of course, there are numerous regulations on chemicals already in place, applied at a national and EU-wide level, which industries like ours have an excellent record of complying with. But the CSS points out that with global chemicals production expected to double by 2030, and with the number of new chemicals continuing to rise, a more radical approach is needed to prevent citizens and the environment from being exposed to potential harm.
-
What’s involved in this more radical approach?
Quite a lot of it comes down to chemical regulations. So plans are being put in place, for example, to tighten existing restrictions on carcinogens, mutagens and reproductive toxins (CMRs). At the same time, new restrictions will be introduced on chemicals that research has indicated are of concern, such as endocrine disruptors and per- and polyfluoroalkyl substances (PFAS). And the lists of chemicals in these categories, and others, are growing as evidence mounts over the long-term effects on certain chemicals previously thought to be relatively benign – so it’s an ever-changing landscape.
And in addition to this, measures will be put in place to encourage innovation to develop safer alternatives that are ‘sustainable by design’. This includes not just attending to safety profiles, but looking at products more holistically, for example reducing their carbon footprint, or making them easier to recycle as part of a circular economy.
-
Why does the CSS have particular relevance to automotive interiors?
It comes down to two factors. The first is the number of materials used in car interiors, particularly fabrics, carpets, leather, foams and polymers, all of which typically use a range of chemicals in their production, and which have the potential to come into contact with the driver or passengers. Secondly, it’s the confined nature of the car cabin, which can lead to a build-up of the more volatile chemicals, and consequently poor air quality.
-
But isn’t the industry already on top of issues around volatile emissions into car cabins?
Yes, it certainly is – those in the industry will be well aware of discussions around the ‘new car smell’ dating back to the early 2000s, and the subsequent moves to develop materials with low levels of harmful volatile organic compounds or VOCs, alongside analytical methods to quantify them.
But that’s only part of the story, because the chemicals that are increasingly of concern often aren’t that volatile, but they can get into our bodies or into the environment in other ways – and that more holistic viewpoint is what the CSS is putting in place.
-
So do you think that EU regulators will start to overtake OEMs in terms of their importance for setting the trends in chemical content?
Arguably, yes. Historically, most of the impetus for restrictions on chemicals in automotive interiors came from customers and OEMs themselves, and that was passed down the supply chain. Up to now, regulators have trailed somewhat, only stepping in to restrict the most harmful chemicals.
But with the release of the CSS, it’s likely that regulators will start playing a more prominent role, with a broader focus on chemicals that maybe don’t have such a great sustainability profile. So the upshot is that the existing landscape around chemicals in automotive interiors is going to change, and anyone involved in the supply chains will need to be aware of the latest developments.
Plus, it seems likely that the regulations that will come out of the CSS will mean that the allowable levels of chemicals in products sold in the EU will be the strictest worldwide – so it makes sense as a supplier to take our lead from that when it comes to our products.
-
How do you go about formulating products to eliminate chemicals of potential concern?
Sometimes it’s a relatively straightforward process to make a replacement, with little or no loss of functionality or cost-effectiveness. But in other cases, the functionality provided by the chemical in question is such a feature of the process or the product that you need to go back to the drawing board.
For performance tapes, certain solvents are a case in point, because they’re integral to the process of dissolving the adhesive polymer and depositing it as a solution on the carrier film. Finding solvents that can dissolve polymers easily, and that also have relatively low volatility and a high flash point, is really difficult. Plus on top of that you have to bear in mind sustainability and cost-effectiveness.
-
And that’s led you to develop your alternative adhesive technologies?
That’s right. Of course, the solvents we use in our tapes have always met the most strict regulatory requirements, but the regulatory landscape is changing rapidly. To address the issues raised by the CSS, you could go to a lot of effort to replace one solvent with another that’s currently deemed safer. But from a business perspective, in 10 or 15 years’ time that might fall under the regulations too, and then you’re back with the same problem.
So, we thought why not just eliminate these solvents altogether? Let’s take UV acrylics as an example. Instead of polymerizing the adhesive in solvent, and then applying the solvent solution to the carrier film, you can tweak the chemistry of the polymer chains instead so that the polymer is a liquid at elevated temperatures. Then, all you need to do is heat it up, apply it to the carrier film, and it’s ready to be UV-cured. There’s no solvent involved at all, so we end up with a product that is very close to being zero-VOC.
-
And what are these UV acrylics being used for?
Similar solvent-free UV acrylics have been widely used in certain automotive interior applications for quite a while already, but only in applications where their very low VOC content has been essential – such as in seat heating mats. But we know that this technology is straightforward to apply elsewhere in automotive interiors, for example to affix polyurethane foams or polyester fleeces. In fact, the latter is a good example, because unlike polyurethane foam it doesn’t contain isocyanate and is more easily recyclable. As a result, it’s a material that’s likely to become more widely used – so it’s one we’re looking at closely. It’s all about staying ahead of the curve!
-
And what about hotmelt rubbers? Where do those fit in?
Well, excellent though our modified UV acrylics are, they’re not suitable for every automotive interior application, because they don’t adhere so well to some plastic substrates. So to fill that application gap, and avoid the need to go back to solvent-based adhesives, we’ve come up with hotmelt rubbers.
These are rather different chemically, being a rubber mixed with tackifiers, forming a pressure-sensitive adhesive that doesn’t need curing. So as well as instant adhesion, they form a particularly strong bond within the temperature range we’re talking about for automotive interiors. And importantly, they stick really well to plastics, which is very useful given the quantities of plastics used in vehicles these days, especially as we move towards EVs and the trend for ‘lightweighting’ that we’re seeing there.
-
And both these products are CSS-ready, so to speak?
Very much so, and I’d go so far as to say that with our range of performance tapes featuring these modified UV acrylics and hotmelt rubbers, we’ve leapfrogged over the whole CSS situation. Because they’re free of volatile components that could cause concern either now or further down the line, if you’re a Tier 1 or Tier 2 supplier looking to address the issues raised by the CSS, they’re a future-proof solution!
We already have over 40 of these products on the market, so we’ve been leading the way in anticipating the need for safer products in the automotive sector. It’s a case of reassuring customers that the challenges posed by CSS can be overcome, and that there are products on the shelf today that are ready and waiting to be used. Alternatively, of course, we have the technology and expertise to adapt them to a customer’s exact needs.
-
And I understand that’s not all when it comes to sustainability. What else is Avery Dennison doing?
There are a number of strands to our sustainability strategy, of which addressing the chemicals used in our products is just one. For example, one of the reasons why CSS has a focus on reducing or eliminating certain chemicals is to simplify and streamline end-of-life processing of materials, to assist in the development of a circular economy – so our new tapes tick that box, too.
Our performance tapes featuring UV acrylics and hotmelt rubbers also help to move towards a circular economy in another way, by making it easier to deconstruct assemblies that otherwise might have used permanent fixings. Plus there’s the use of recycled and bio-based materials in our products, as well as our drive to reduce greenhouse gas emissions arising from our activities.
So the work we’ve done on solvent reduction in anticipation of the CSS is part of a bigger picture… and one that points to a safer, healthier future for automotive interiors. I’m excited to be part of it!
Market Segments for Automotive Adhesives
Sustainable automotive interior solutions
Automotive interior upholstery relies heavily on specialized adhesives to bring together a variety of materials like polyurethane, EPDM, PVC, TPO, foams, fibers, and metals. At Avery Dennison, we understand the complexities OEMs face in selecting the right bonding solutions for every substrate and environmental condition. Our automotive interior adhesive tapes are designed to meet these challenges head-on, ensuring optimal performance and production efficiency while enhancing the overall driving experience. We stay on top of automotive interior trends, innovating our product lineup to meet manufacturers' stringent requirements and deliver reliable solutions for automotive interiors.
In automotive interior design, Avery Dennison provides innovative solutions to address the challenges of the circular economy. Our UV acrylic and hotmelt performance tapes facilitate easier deconstruction of assemblies that might otherwise rely on permanent fixings. While our proprietary UV acrylics, known for their low VOC content, are ideal for applications like seat heating mats and affixing polyurethane foams, they don't adhere well to certain plastics. To bridge this gap without resorting to solvent-based adhesives, we've developed hotmelt rubbers. We also focus on using recycled and bio-based materials and are committed to reducing greenhouse gas emissions.
Adhesive selection for automotive interiors
Automotive interior suppliers and manufacturers are increasingly challenged to source adhesive tapes that provide suitable performance against this wide range of surfaces. Determining the correct adhesive when bonding to foam and other materials in the automotive upholstery adhesive space may be challenging, especially when seeking to provide your customer an accurate quote quickly and accurately.
To help you with the adhesive selection and the technical requirements your customer may require, Avery Dennison Performance Tapes has developed a series of adhesive bonding studies looking at the performance of our Pressure Sensitive Adhesive solutions when combined with foams and other materials from industry leading manufacturers.
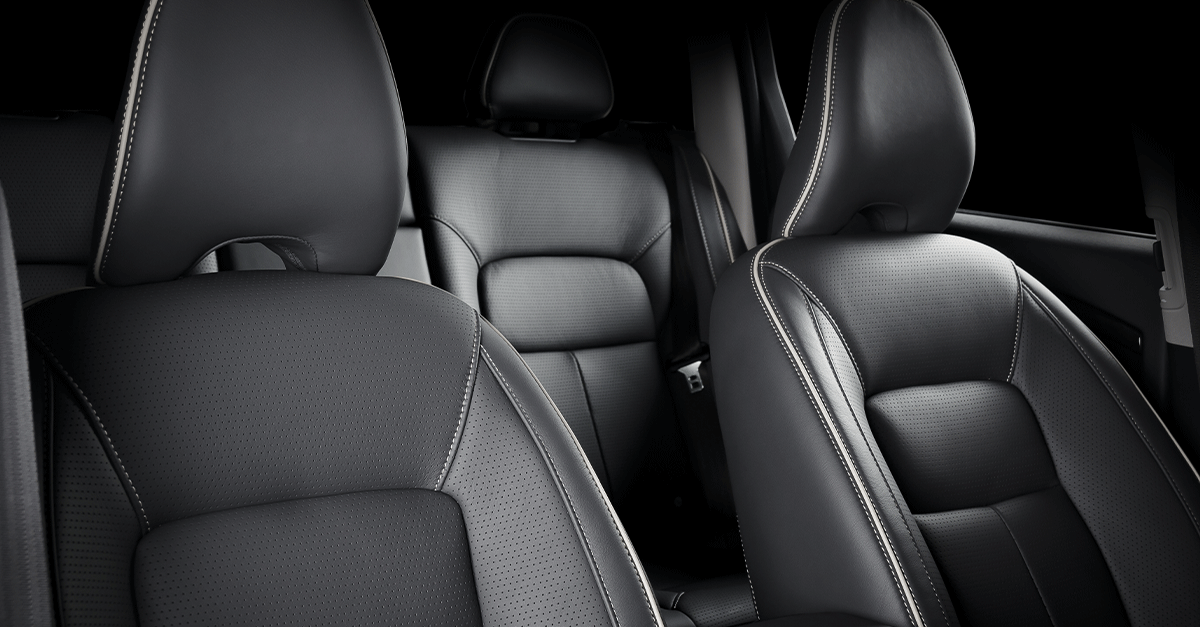
Automotive upholstery
With decades of experience in the automotive industry, our Performance Tapes business, established in the 1960s, has evolved to provide advanced adhesive solutions for a wide range of car interior applications.
We collaborate closely with OEMs, tier suppliers, and converters to address engineering challenges and design requirements, developing reliable solutions tailored to the increasingly advanced materials used in automotive interiors. Our focus isn't just on offering products, but on delivering solutions that meet the industry's growing needs.

Technical support
Customers selecting our automotive laminating and bonding tapes benefit from our technical support. We grasp the intricacies of designing and manufacturing automotive interiors, offering solutions and assistance both on-site and remotely.
Our custom solutions address diverse needs and future requirements. We pride ourselves on this customization and our ability to provide the ideal solution. By choosing Avery Dennison, OEMs, engineers, converters, and suppliers gain confidence in adhesive systems backed by a global materials science leader to ensure timely product availability.