Advanced Adhesive Solutions for Heat Shields
As automotive technologies continue to advance, effective heat management has become a critical design consideration. The push toward vehicle electrification, the rise of turbocharged smaller engines, and the growing emphasis on lightweight construction have all contributed to increased thermal loads in modern vehicles. To meet these challenges, manufacturers are moving away from heavy, metal-based heat shields and embracing lightweight, adhesive-based solutions that simplify assembly and improve long-term performance. That’s why many automotive manufacturers and suppliers now rely on lightweight, “peel and stick” heat shields that can also contribute to improved NVH (Noise, Vibration and Harshness) performance.
How Adhesives Are Transforming Heat Shield Applications
Modern heat shields must do more than just block heat. They need to be lighter, more adaptable, and easier to install than ever before. Adhesive technologies play a vital role in achieving these goals. Instead of relying on traditional fasteners like bolts and rivets, manufacturers are now choosing pressure sensitive adhesives that create a continuous bond across the surface of the heat shield.
These advanced adhesives deliver secure bonding to challenging surfaces and offer the durability to withstand harsh operating environments. Exposure to extreme temperatures, chemicals, and environmental conditions is no problem for today’s high performance adhesives, which maintain their integrity over years of continuous vehicle use.
High Performance Adhesives for Demanding Heat Shielding
At Avery Dennison, we offer a range of adhesive solutions specifically engineered for the demands of modern heat shielding applications. These adhesives are field tested and meet stringent OEM specifications, providing reliable performance where it matters most.
Recommended Adhesives for Heat Shielding:
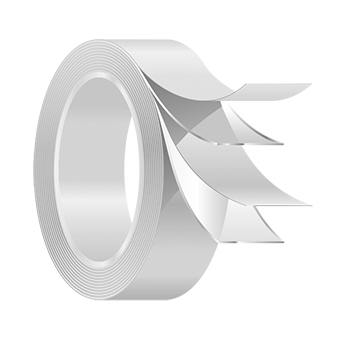
FT 9220
Avery Dennison FT 9220 is a double coated tape with high initial tack and a modified acrylic adhesive, offering excellent resistance to chemicals, moisture, and UV light. Ideal for point of display systems, automotive interiors, white goods assembly, and general industrial bonding where strong initial adhesion and easy removal are required.
- Ensures an immediate initial adhesion
- Consistent application performance
- Excellent resistance to solvents, chemicals, plasticizers, moisture, temperature and UV-light
- Facilitates easy removal at point of display
- Easy die-cuttable and stable liner
- Provides exceptional conformability
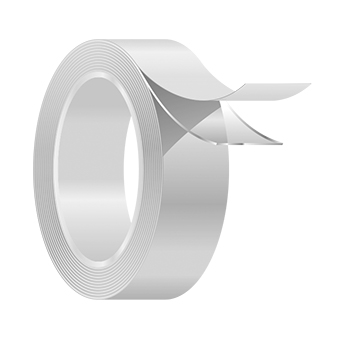
FT 125
Avery Dennison FT 125 is a 90µm modified acrylic transfer tape that provides high adhesion to a variety of substrates (including low surface energy plastics), excellent resistance to UV light and high temperatures and easy unwind and liner removal. FT 125 is designed for use in security, automotive, label and foam and fiber bonding applications.
- Ensures an immediate initial adhesion
- Consistent application performance
- Good conformability to flat or curved surfaces
- Excellent resistance to solvents, chemicals, plasticizers, moisture, temperature and UV-light
- Facilitates easy removal at point of application
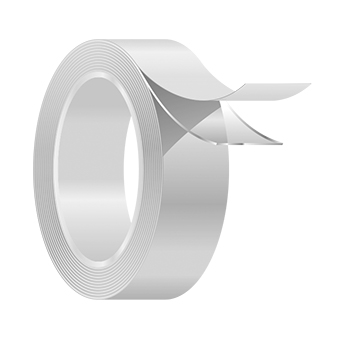
HPA 2922
Avery Dennison HPA 2922 has a white polyethylene protected paper with red “Avery Dennison” imprint. It facilitates easy removal at point of application and combines a high degree of moisture stability with excellent die-cutting properties.
- Ensures an immediate initial adhesion on wide range substrates, especially plastics
- Outstanding resistance to solvents, chemicals, plasticizers, moisture, temperature and UVlight
- High temperature holding power
- Excellent adhesion on wide range of substrates, including LSE surfaces
- Facilitates easy removal at point of application
- Combines a high degree of moisture stability with excellent die-cutting properties
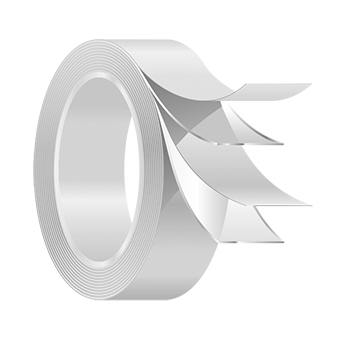
HPA 9353
Avery Dennison HPA 9353 was designed for bonding to a wide variety of engineered plastics, metals, paints and urethane foam substrates.
- Ready made for die cutting
- Ease in slitting and processing
- Elevated temperature, plasticizer and solvent resistance
- Good foam bonding characteristics / improved with heat lamination
Adhesive Solutions That Outperform Traditional Fasteners
Adhesive based solutions provide distinct advantages over mechanical fasteners in heat shield assemblies. Unlike bolts and rivets, adhesives distribute stress evenly across the entire bonded area, reducing the risk of tearing and fatigue failures often seen in traditionally fastened shields.
Adhesives also help prevent galvanic corrosion, which can occur when metal fasteners interact with aluminum heat shields. By eliminating these metal fasteners, adhesives not only improve product longevity but also contribute to cleaner, more efficient assembly processes.
Partner with Avery Dennison for Heat Shielding Success
Easy assembly and high productivity are key to success in the high volume automotive industry, and PSA solutions lend themselves well to manual and automated methods. As many heat insulting materials are fragile, we engineer solutions where liner removal is facilitated either through selected liner release coatings or by pattern coating so that every diecut part presents a fingerlift.
From improved durability to faster, more flexible manufacturing, adhesive technologies are setting new standards for heat shielding performance. Backed by field proven solutions and unmatched technical support, Avery Dennison is ready to help you solve the toughest thermal management challenges in modern vehicle design.
Contact your Avery Dennison account manager or visit our website to learn more about advanced heat shielding solutions for the automotive industry.
About the author
Jarne Machiels
Application & Technical Service Engineer
Jarne Machiels is the Application & Technical Service Engineer responsible for Germany as well as (Automotive) Electronics Market at Avery Dennison Performance Tapes Europe. Thanks to his previouses roles in the printing - and adhesive tape converting industry, he has an extensive know-how to understand your technical needs for each application. In parallel, Jarne focuses on technical innovation within Avery Dennison - being expertised in (printed) electronics, heating applications and automotive safety systems.
jarne.machiels@eu.averydennison.com
www.linkedIn.com/in/jarne-machiels