Feature: EV Segment Picks Up Speed at The Battery Show 2022
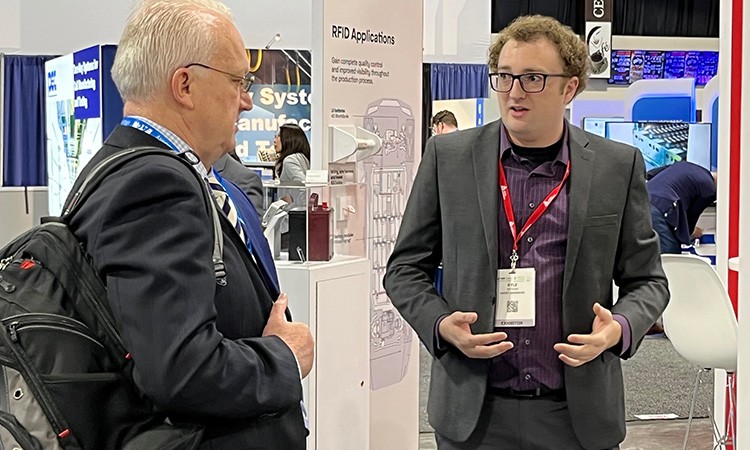
The EV battery marketplace is attracting much investment. As this segment grows, there’s also a sustained need for engineering expertise, solutions and scalability. The Battery Show North America, held in Novi, Michigan, September 13-15, was proof of this. Sold out for exhibitors and attendees, the show hosted more than 10,000 people including representatives from the major automotive OEMs and tier suppliers. It was really a “who’s who” of the EV and EV battery value chain.
Avery Dennison Performance Tapes was one of the show’s more than 800 exhibitors. Our booth showcased not only our pressure-sensitive adhesive tape products but solutions from our Avery Dennison Smartrac and Label and Packaging Materials business units.
The booth was a bustling place. We welcomed the opportunity to meet and listen to many show visitors and discuss our portfolio and services.
Notes from the show floor: my obersvations
I also walked the floor and compared notes with other members of the Performance Tapes team. Now, a few days after the show has wrapped up, I’ve boiled down all I saw into three key observations.
The two major areas of focus for EV battery engineers are flammability prevention/mitigation and dielectric management.
EV manufacturers are working hard to break the stigma that batteries are highly flammable. The truth? Gasoline vehicles are far more likely to catch fire. But when an EV goes up in flames, it tends to be more likely to make the news … and stay there.
As OEMs and EV battery manufacturers have faced scrutiny over flammability issues, they’ve made flame retardancy a priority. Many are now incorporating a variety of materials in their batteries designed to prevent thermal runaway (an event where a single overheating cell causes other cells to overheat, leading to a chain reaction), and mitigate fires.This leads to my second observation...
Functional materials — often combined with pressure-sensitive adhesives — are solving significant engineering challenges and enabling the next generation of EV battery design.
EV battery packs are evolving to become more compact, with less space between cells. This space constraint challenges engineers working on problems such as thermal runaway, dielectric management, cell padding/shock absorption and general bonding.
In response, designers are creating multi-functional laminated structures (composites) with integrated functional materials. These composites are gaining popularity for their effectiveness and design flexibility within these tight spaces.Pressure-sensitive adhesives are often a vital element of these composites. Adhesives not only provide reliable bonding but can be engineered with properties such as dielectric strength and flame retardance (meeting UL® 94 V-0 requirements). In fact, two of the newest additions to the Avery Dennison EV Battery Portfolio address these issues. More on those in a bit.
Finally …
The EV space is evolving quickly. The ability to solve problems fast, up and down the value chain, is at a premium.
You only need to look at the headlines to know the EV marketplace has built tremendous inertia. The Inflation Reduction Act (IRA) includes a $7,500 credit for EV purchases and a $7.5 billion investment in charging infrastructure across all 50 states. California, meanwhile, has announced that 100% of cars sold in the state by 2035 must be zero-emission. And OEMs will invest more than half a trillion dollars into EV innovation by 2030.
According to the International Energy Association, 120,000 EVs were sold worldwide in 2012. In 2021, more than that number were sold each week! As growth accelerates, engineers are working fast to address issues not only with battery and vehicle design but with charging and other areas of infrastructure. They need — and will continue to need — fast and effective solutions that can be scaled quickly.
Bonus observation: Our newest EV Battery Portfolio products generated much interest
Back at our booth, we were excited to show off two new products designed specifically for the needs of modern EV batteries.
Conformable Dielectric Film has stretch and relax properties that allow it to conform to the raised contours and unique geometries increasingly found in EV battery packs. Engineered as an alternative to spray coatings, this film has applications on cold plates, chiller fins, pack enclosures and structural
Flame ToughTM Rubber Adhesive builds on the innovation offered through our Flame Tough platform, this time in a rubber-based formulation. The new adhesive offers higher levels of adhesion and tack. It’s also halogen-free, helping address a growing concern in the industry.
About the author:
Max VanRaaphorst is business development manager – E-mobility and Automotive, Avery Dennison Performance Tapes North America. With nearly a decade of technical, sales and marketing experience in the chemical manufacturing field, Max strives to help Avery Dennison tape converters grow their business in the fast-evolving E-mobility and Automotive segments. Based in Michigan, he can be reached through LinkedIn.