Electric Vehicles are Poised to Take Charge
Pressure-sensitive adhesive tape constructions are helping solve some of the industry’s most vexing EV challenges
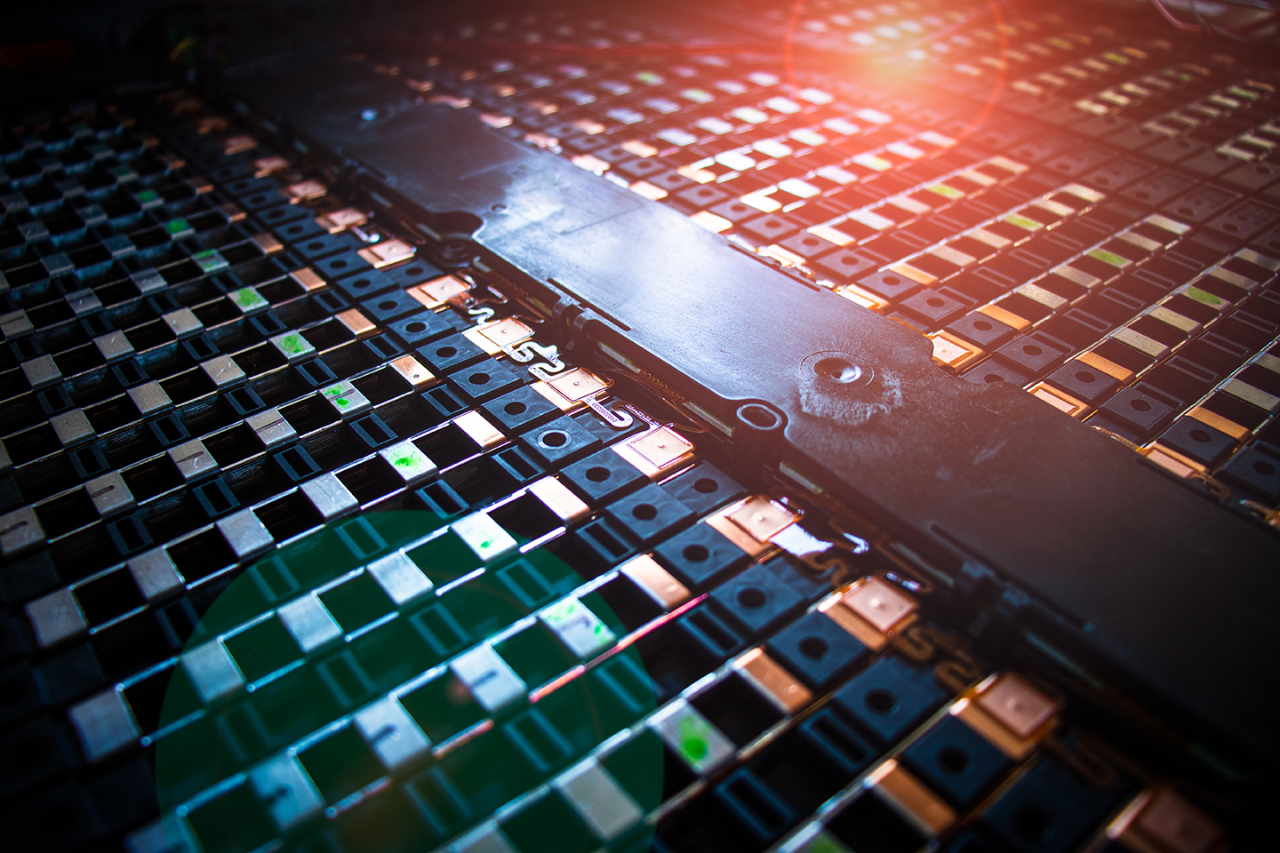
Way back in 1886, a German engineer named Karl Benz began commercial production of the first cars with gasoline-driven internal combustion engines (ICE). Since then, automotive styling has changed dramatically, and technology has evolved to make cars safer, more reliable, faster, and more efficient.
But in many essential ways, today’s ICE vehicles are the direct descendants of the earliest gasoline-powered cars: four wheels (Benz’ actually had three, but four eventually became the standard); steering and braking controlled by mechanical or hydraulic linkages; and at their heart, engines that create power from dozens of explosions of fossil fuel vapor and oxygen every second.
We are now entering an era in vehicle development that truly changes the definition of the automobile. Cars are no longer undergoing an evolution, but a revolution. More drivers are taking a pass on the ICE in favor of electric motors powered by state of the art battery packs. It has been just 12 years since Tesla introduced its first Roadster model (one of which is now orbiting the sun, intersecting the orbits of Earth and Mars), and electric vehicles are about to go mainstream.
As an October 2020 article in Forbes states: “If the high stakes and recent, almost universal rush by manufacturers to bring fleets of wholly practical EVs to market is a meaningful indicator, we’re fast approaching the EV tipping point. What lies beyond is a future where electric cars are the default and gasoline-powered cars are relics of a carbon intensive past.”
We have kept our eyes on the EV space for many years, because we know it is one that will provide tremendous opportunity to converters and others working with high-performance, pressure-sensitive adhesive tapes. More on that in a bit.
What is powering this electric revolution?
According to Cowen and Company’s September 2020 report, “Future of Mobility Primer,” EVs are expected to achieve a 9.5% market share by 2025, and 25.7% by 2030 (see chart). This dramatic rise will be powered by several trends.
Costs: EVs will become more affordable than ICE vehicles at some point in the early 2020s. This will be due to a reduction in the cost of battery technology, and an increase in the cost of ICE technology related to carbon emission and fuel-efficiency requirements.
Policy: Policy makers in the U.S. and abroad are enacting measures to accelerate the adoption of EVs. As an example, the state of California has recently announced a ban on the sale of ICE vehicles in the state by 2035. Several European nations, along with the UK, have announced phase outs of new ICE vehicle sales. Most are set to start in 2025 or 2030.
OEM aspirations: In response to a variety of factors, including changing consumer tastes and the regulatory activity explained above, more OEMs are setting time-bound goals to be exclusively electric. General Motors just announced its plan to be all-electric by 2035. Volvo now offers electrified (including hybrid) versions of all its models, and has a goal to have 50% of its sales volume be fully electric by 2025.
Innovation: Battery technology is improving quickly. EV range is increasing — and is expected to continue to increase — while charging times decrease. Other consumer “pain points” related to early EV batteries are being addressed by engineers, and they are making progress.
For example: A standard Tesla Model 3 retails for $33,690 with EV incentives. It has a published range of 263 miles, a 200-mile charging time of 15 minutes at one of the company’s 20,000 Superchargers, and a very respectable 0-60 time of 5.3 seconds. That’s a fully electric car in the same ballpark as a similarly-sized ICE vehicle for cost, convenience and performance.
What is the opportunity for pressure-sensitive tapes and adhesives?
Whether or not you are excited about the passage into history of the ICE, the fact remains the converting and tape industry is really poised to grow with the EV revolution.
EV batteries have a range of applications for converted, pressure-sensitive materials that enable those packs to be more efficient, safer and easier to assemble. In fact, pressure-sensitive materials are suited for providing solutions for some of the most vexing challenges that have faced battery pack manufacturers as they have raced to improve their technology.
We have identified several specific EV battery applications that are primed for converted, pressure-sensitive materials:,
Cell to Cell Bonding — Materials that provide structural integrity in pouch and/or prismatic battery cells
Thermal Runaway Protection — Materials dedicated to the prevention of thermal runaway events in which a domino effect of fire spreading from cell to cell can occur
Flexible Busbars — Flexible, printed circuits that require electrical insulation and flame resistance
Thermal Interface Materials (TIMs) — Materials that assist with battery module cooling
Electrical Insulation — Electrically insulative materials throughout a battery pack
Compression Padding — Materials to protect individual cells from damage caused by impact, movement, or swelling
Pack Seal and Gasketing — Materials to create watertight seals between battery casings and rubber gaskets
These applications all have varying requirements for factors such as dielectric strength, flame retardancy, bond strength and more. Composites made with foams, fibers, films and pressure-sensitive adhesives are thus being used for temperature control, flame barriers, electrical insulation, cushioning and bonding of battery pack components.
And besides offering the specific properties needed for these applications, these materials are easy to apply/assemble, provide a slim profile, and a continuous bond across a large surface area.v They are also generally lighter than mechanical fastening systems — important in an industry that is looking for ways to reduce battery pack and overall vehicle weight.
A long history, a bright future
Avery Dennison has a long history in the automotive industry. Since the inception of our Performance Tapes business unit in the 1960s, our Automotive Portfolio has evolved with solutions for a wide range of applications — applications that have evolved with vehicles themselves. We have worked (and continue to work) closely with OEMs, tier suppliers, and converters to understand engineering challenges, design requirements and growth opportunities. And we have collaborated with these parties to develop effective and reliable solutions.
As proud as we are of this history, we are even more excited about the industry’s future. So it follows that we are staying in step with the industry as it undergoes this EV revolution.
We welcome a leadership role in helping the industry adopt pressure-sensitive adhesive tapes to EV applications. Our EV Battery Portfolio will grow over time, and change as the needs of the industry change. The bottom line is that you can count on Avery Dennison to provide the solutions you need, when you need them.
Learn more about our EV Battery Portfolio at tapes.averydennison.com/evbattery.
About the author:
Michael VanHaerents is an automotive segment business development manager for Avery Dennison Performance Tapes. He leverages nearly 20 years of adhesive and sealant engineering and program management experience in the automotive industry to help build strategic relationships, create product specifications, and build new technology portfolios for new and existing adhesive and tape applications. Based in the Detroit area, he can be reached at michael.vanhaerents@averydennison.com, and welcomes your connection on LinkedIn.