Feature: Behind the Mirror
OEMs and suppliers increasingly rely on adhesive mirror bonding solutions for their automotive assemblies.
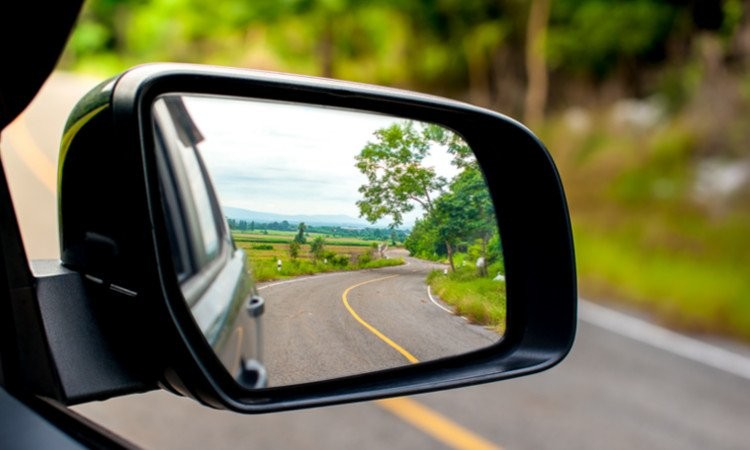
Here’s a conversation starter: The first use of an automotive rear view mirror was in the inaugural Indianapolis 500, in 1911. Driver Ray Harroun used one to keep an eye on his rivals during the grueling race. That mirror turned out to be an advantage. He won that day, and earned a place in automotive history.
The rear view mirror became common as a safety feature on passenger cars later during the 20th century. But for years, little had changed technologically from the mirror Harroun used at the Brickyard. Now, with the dawn of connected and computerized vehicles, both exterior side view and interior rear view mirrors have undergone an evolution.
More than meets the eye with mirror bonds
Modern mirror assemblies can house a variety of electronics and mechanical components related to driver safety and comfort. Exterior side view mirrors commonly house heating elements that keep them ice- and fog-free. They may have sensors or cameras that are part of a vehicle’s proximity alert system, and a LED integrated into the mirror as part of the vehicle’s lane change warning system. Interior rear view mirrors frequently come with an auto-dimming feature, and may house readouts for vehicle information.
Fact is, the mirrors in modern cars are often a tight package of expensive components. With cars being driven longer and harder than ever before, they have to be built to last. And with OEMs continually on the hunt for ways to improve margins while saving weight and increasing quality, many now certify PSA adhesive solutions in their mirror specifications. Many of those solutions come from Avery Dennison.
Key mirror bonding characteristics to keep in your view
The following are a variety of mirror bonding performance attributes that are important to OEMs and Tier suppliers:
Secure component bonding with no heat or cure time, which can reduce assembly time and improve manufacturing flexibility.
Excellent adhesion to glass, ABS, and other materials commonly found in mirror assemblies.
Ability to withstand temperature extremes, high and low.
Excellent gap-filling properties for rough and uneven surfaces.
Ease of use for converters. Avery Dennison solutions are easy to die cut, including into pads and small pieces.
The foundation of our portfolio is a collection of high-performance adhesives that are relied on by many in the industry. These adhesives are offered in a variety of tape constructions. Depending on the application, they can be laminated to thin or thick foams, plastic films, or ordered as a transfer tape.
A virtually off-the-shelf solution
Importantly, our mirror bonding products meet a wide range of OEM specifications, so they’re ready for use with minimal testing or hassle. They are backed by extensive service and testing capabilities in our ISO and UL® certified laboratories.
Avery Dennison adhesive solutions give converters an advantage to win in this dynamic and evolving application. We think even Ray Harroun would appreciate that.
To learn more about our adhesive tape solutions for automotive mirrors, visit our automotive mirror solutions page or contact your account manager.