On the Floor at the 2019 Battery Show
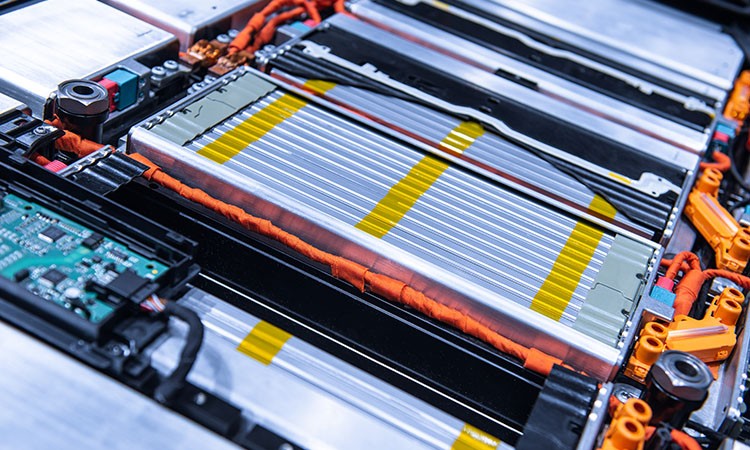
I recently attended the 2019 Battery Show in Novi, Michigan along with my colleague, Scott Krusinski, senior design and application engineer. Billed as North America's largest and most comprehensive advanced battery manufacturing trade show, the annual event now brings together 650 suppliers, plus engineers and battery technology innovators.
The show truly has global importance, as BEV growth is a fast-moving trend in the North American, European, and Asian auto markets. For us, the show was an opportunity to get an even deeper understanding of the rapid evolution of battery technology. We also welcomed the chance to discuss with engineers and designers about how they might leverage pressure-sensitive adhesives to help solve their current and future challenges.
I think I speak for both Scott and I, when I say our biggest overall impression is just the incredible progress being made in BEVs. At every turn, we saw more reasons to believe the many expert predictions that the global vehicle market is going to grow to become electric, with a tipping point within the next decade to 15 years. To this point, in his conference-opening Keynote, Bob Galyen, chief technology officer of CATL, highlighted a prediction of 24% CAGR for lithium-ion battery packs, according to AVICENNE Energy. The biggest portion of that growth is predicted to come in automotive and bus.
Many factors are allowing this to happen. Some of the development trends we witnessed at the show included:
Trend toward solid-state lithium-ion batteries
We were impressed by the growing focus on sulfide-based, all solid-state batteries (ASSB). Solid-state batteries possess a higher energy content than comparable liquid electrolyte batteries. They’re also safer, with decreased fire risk. We should expect a decade for ASSB technology to be scaled and available at a lower cost. But it’s something we are keeping an eye on.Innovation in battery venting
All battery packs generate heat, causing the air inside them to expand. For obvious reasons, this air pressure needs to be safely vented. Passive, PTFE-based venting solutions have been developed to allow the battery release this pressure without moisture being allowed in. A new offering from Gore, presented at the show, features this passive technology with the addition of an active vent that enables mass venting in case of a fire.
Evolution of lithium-ion battery cooling technology
We’re seeing a desire by OEMs and battery manufacturers to move away from active cooling systems (water- and air-based) for battery packs, and toward passive systems using heat conductive materials. One such system uses an adhesive-backed thermal compression pad placed within the battery pack. This allows cells and battery modules to lower thermal impedance to the bottom of the pack to assist with cooling.
Thermal runaway protection
Morgan Advanced Materials gave an excellent presentation on the effect of thermal runaway at the cell level. China has adopted a test method, currently called the GB standard, that requires a battery pack to burn for a specific amount of time without initiating a thermal runaway event. As lithium-ion batteries are asked to do more and more, expect this issue to get increasing attention.
Much engineering progress has been made, and much remains. This electric future depends on the mass production of powerful, reliable, widely affordable, and durable batteries. Battery engineers and designers will be grappling with key issues related to materials, including electrical insulativity, flame resistance, thermal management, and automotive grade protection.
Many of these issues can be addressed, at least in part, with adhesive materials. Avery Dennison offers more than 100 formulas with technologies that address extremes of high temperature, vibration, impact, thermal runaway. These include solutions for battery venting, emerging technologies such as ASSB, and thermal impedance adhesives for passive cooling. Many of our adhesives and tape constructions can be customized to meet ULⓇ 94 V and other requirements for thermal runaway material bonding applications. And we can create unique constructions featuring PU foams, electrically insulative films, or other materials.
About the author:
Michael VanHaerents is an automotive segment business development manager for Avery Dennison Performance Tapes. He leverages 17 years of adhesive and sealant engineering and program management experience in the automotive industry to help build strategic relationships, create product specifications, and build new technology portfolios for new and existing adhesive and tape applications. Based in the Detroit area, he can be reached at michael.vanhaerents@averydennison.com, and welcomes your connection on LinkedIn.